|
Search Resources (6 Results)
 |
|
Other | Approved: 7 years ago | 297.54 kB | Comments: 0
...Professor/Instructor: Type of the Report: ? Individual,... ...Simulink of Matlab: The time constant is... ...critical parameter of system which obey first... ...from Figure1 below, the response of the... ...the response of the system when a... ...response of the system when a time... ...at time=40 while the response of the... ...the response of the system when a... ...response of the system when a time... ...2 below. Therefore, the system response faster... ...below. Therefore, the system response faster at... ...time constant=3 than the time constant=7. Figure... ...1: Plot of the first order transfer... ...2: Plot of the first order transfer... ...3: Plot of the second order transfer... ...4: Plot of the first order transfer...
| N/A |
161
|
cloveb
|
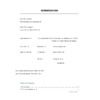 |
|
Other | Approved: 7 years ago | 933.11 kB | Comments: 0
...Professor/Instructor: Type of the Report: ? Individual,... ...1 Diagram of the equipment present in... ...heat exchanger control system (2) .................................... 6... ...2 Diagram of the system with additional... ...Diagram of the system with additional inputs... ...with Ti=50s-1 and the Proportional Integral Controller... ...with Ti=50s-1 and the Proportional Integral Controller... ...is one of the widely used in... ...between each other. The first objective in... ...was to analyze the co-current behavior of... ...done by changing the response of the... ...the response of the system regarding a... ...response of the system regarding a step... ...step change in the steam percentage from... ...65% to 100%. The second objective was... ...was to investigate the performance of different... ...response were compared. The results of the... ...The results of the comparison between the... ...the comparison between the different types and... ...controller proved that the PID controllers are... ...PID controllers are the best types of... ...controllers to predict the behavior of a... ...behavior of a system and to provide... ...response for approaching the desired set point.... ...space and aren’t the most efficient type... ...of heat exchangers. The name derive from... ...which refer to the fluid flow directions... ...was flowing on the shell side. Proportional,... ...process information and the desired set point... ...on these errors the controller actuates in... ...controller actuates in the process to make... ...process to make the controlled variable reach... ...controlled variable reach the set point (1).... ...(1). Figure 1shows the function of a... ...Figure 2 shows the transfer function of... ...in Laplace domain. The parameters of a...
| N/A |
222
|
cloveb
|
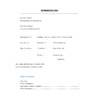 |
|
Other | Approved: 7 years ago | 6.81 MB | Comments: 0
...Professor/Instructor: Type of the Report: ? Individual,... ............................. 13 Introduction The main objectives of... ...were to study the performance of the... ...the performance of the proportional-integral (PI) and... ...controllers in controlling the 1 liquid level... ...a tank using the Cascade control system... ...the Cascade control system via LabView and... ...LabView and investigate the properties of the... ...the properties of the open and closed... ...closed control loops. The selection of proper... ...was assisted through the use of LabView,... ...design for control system. The simulation package... ...for control system. The simulation package was... ...in cascade mode. The performance of the... ...The performance of the different type of... ...examined by adjusting the tuning parameters Kc,... ...In this experiment, The Multi-Process Control Trainer... ...complete process control system using cascade control... ...using cascade control system. The simulation process... ...cascade control system. The simulation process involved... ...simulation process involved the tuning of the... ...the tuning of the PI and PID... ...controllers to control the liquid level of... ...liquid level of the lower and upper... ...a set point. The main objective of... ...objective of using the PI and PID... ...was to investigate the control response of... ...control response of the system and reduce... ...response of the system and reduce the... ...system and reduce the effect of various... ...disturbances such as the change of the... ...the change of the liquid level rate... ...level rate in the system. However, the... ...rate in the system. However, the control... ...the system. However, the control process was... ...order to accelerate the response of the... ...the response of the control process, and... ...and 0.010 for the Ti in order... ...might occur in the control system. The... ...in the control system. The PID parameters... ...the control system. The PID parameters were... ...in this control system to obtain the... ...system to obtain the liquid level set... ...of 20% for the upper tank and... ...and 10% for the lower tank. The... ...the lower tank. The three control setting... ...parameters used throughout the experiment for PID... ...and Ti= 1.3. The experimental result was... ...Ti to illustrate the effect of the... ...the effect of the tuning parameters on... ...tuning parameters on the control system at... ...on the control system at different time... ...controlling a process system, feedback controllers are... ...process by determining the action 2 needs... ...needs to control the process variable. To... ...In this experiment, the upper tank and... ...controller after allowing the system to reach... ...after allowing the system to reach to... ...feedback controller sends the output information back... ...information back to the controller in order... ...set point. When the liquid level was... ...was higher than the set point, the... ...the set point, the valves were opened... ...opened to reduce the level by allowing... ...level by allowing the liquid to flow... ...flow out of the tank. Alternatively, when... ...tank. Alternatively, when the liquid level was... ...level was below the desired set point,... ...an order by the controller is sent... ...sent to close the valves and allow... ...valves and allow the liquid level to... ...this is called the reverse action controller.... ...monitor and record the data for both... ...for both tanks. The mechanism is continues... ...is continues until the system reaches stability... ...continues until the system reaches stability and... ...both tanks reaches the set points. This... ...done by calculating the error between the... ...the error between the controller variable value... ...variable value and the desired set point... ...be represented by the following equation: ...
| N/A |
215
|
cloveb
|
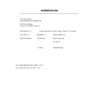 |
|
Lecture Notes | Approved: 7 years ago | 1.79 MB | Comments: 0
...Professor/Instructor: Type of the Report: ? Individual,... ...State Flow Sheet System When Heat Supplied,... ...Dynamic Flow Sheet System When Heat, Q=1000... ...Technology Inc., 2015). The Aspen HYSYS is... ...process chemical plants. The objective of this... ...design and determine the effect along with... ...effect along with the functionality between different... ...and controlled by the use of PID... ...separation unit using the ATV method (Dhib... ...(Dhib R, 2013). The PID controllers is... ...in most of the control system industry.... ...of the control system industry. The controller... ...control system industry. The controller attempts to... ...attempts to minimize the error that may... ...may occur in the process by adjusting... ...process by adjusting the process variable trying... ...to keep at the set point. However,... ...set point. However, the PID controller used... ...control and calculate the vessel pressure as... ...as well as the liquid level percentage.... ...liquid level percentage. The process variable set... ...used to control the process are the... ...the process are the input values of... ...input values of the process. With the... ...the process. With the use of the... ...the use of the HYSYS dynamic simulation,... ...HYSYS dynamic simulation, the system will be... ...dynamic simulation, the system will be identify... ...be identify as the controller will be... ...be operated using the tune mode as... ...as well as the script charts. The... ...the script charts. The result of the... ...The result of the experiment that the... ...the experiment that the PID controller is... ...PID controller is the most accurate and... ...chemical industry over the Proportional and Proportional... ...Controller due to the functionality of it... ...32 constant on the process in reaching... ...process in reaching the steady state. However,... ...steady state. However, the addition of energy... ...of energy to the control showed a... ...minimum effect on the controller process. Page... ...in most of the chemical process industry... ...industry that involve the manufacturing of very... ...Since most of the chemical processes are... ...occur. A such, the chemical process are... ...dynamic in nature, the selecting for the... ...the selecting for the type of a... ...of a control system is very critical... ...and efficient of the process. Therefore, feed-backward... ...value continuously as the differences between the... ...the differences between the desired set point... ...set point and the process variable by... ...by computing both the derivative and the... ...the derivative and the integral of the... ...the integral of the signaled error. A... ...controller (PI); on the other hand, is... ...another type of the PID controller in... ...controller in which the derivative factor of... ...derivative factor of the error is not... ...more accurately in the simulation dynamic mode... ...polynomial interpolation in the vicinity of the... ...the vicinity of the operating point. The... ...the operating point. The PID process variable... ...is defined once the PID controller placed... ...controller placed onto the PFD as shown... ...as shown in the equation below: ...
| N/A |
160
|
cloveb
|
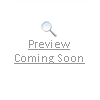 |
|
Solutions | Approved: 7 years ago | 40 kB | Comments: 0
...car horizontally off the top of a... ...3.0m/s. Each of the steps is 0.18... ...Which step does the car hit when... ...are initially at the far west side... ...west side of the circular track and... ...(a) What is the speed of your... ...you have traveled the circumference of the... ...the circumference of the track (b) At... ...point, what is the radial acceleration of... ...car (c) At the same point, what... ...point, what is the total acceleration 3.... ...as shown in the diagram. If we... ...no friction in the system, (a) Find... ...friction in the system, (a) Find the... ...system, (a) Find the acceleration of the... ...the acceleration of the sugar. (b) If... ...sugar. (b) If the system is released... ...(b) If the system is released from... ...how far will the sugar travel in... ...(c) What is the speed of the... ...the speed of the mass after 0.20...
| N/A |
247
|
Guest
|
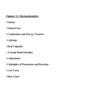 |
|
Solutions | Approved: 7 years ago | 1.72 MB | Comments: 0
| N/A |
138
|
nineandahalf
|
|
Post your homework questions and get free online help from our incredible volunteers
|